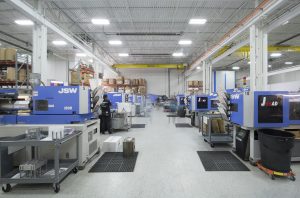
4 Plastic Molding Processes
We are frequently asked about different plastic molding processes and how each effect the process of part design and production. In this post we explain the basics of 4 plastic molding processes: plastic injection molding, blow molding, rotational molding, and vacuum molding.
Plastic Injection Molding
Xcentric Mold specializes in plastic injection molding for low-volume and prototyping. Injection molding is one of the most versatile manufacturing processes. It is used for producing simple and complex plastic parts for nearly every industry.
The injection molding process involves injecting molten material into a mold. The, material is fed into a heated barrel, mixed (using a helical shaped screw), and injected into a mold cavity. Finally, the material cools and forms the plastic part.
Not all materials heat (or cool) the same.
When designing for plastic injection molding, material selection is a critical for success. After all, materials do not all perform the same – during or after the injection molding process. To achieve the intended fit, form, and function of your part design, work with your supplier to choose the optimal material.
The injection molding process can be performed with a host of materials including: plastic, metal (for which the process is called die-casting), glass, elastomers, confections, and most commonly, thermoplastic and thermosetting polymers.
Common examples of plastic injection-molded parts include medical equipment and medical devices, automotive, marine, industrial, agriculture, aerospace and tight tolerance parts.
Other Molding Types
Below are some molding types which are not specialties of Xcentric Mol. However we may be able to provide you with recommendations of other suppliers who can assist you.
Blow Molding
Blow molding is a specific manufacturing process by which hollow plastic parts are formed and can be joined together. In general, there are three main types of blow molding:
- Extrusion blow molding
- Injection blow molding
- Injection stretch blow molding
The blow molding process begins with melting down the plastic and forming it into a parison or in the case of injection and injection stretch blow molding (ISB) a preform. The parison is a tube-like piece of plastic with a hole in one end through which compressed air can pass.
The parison is then clamped into a mold and air is blown into it. The air pressure then pushes the plastic out to match the mold. Once the plastic has cooled and hardened the mold opens up and the part is ejected.
Common examples of blow molding products include bottles, containers and other hollow shapes.
Rotational Molding
Rotational molding is comprised of a heated hollow mold which is filled with a charge or shot weight of material. It is then slowly rotated (usually around two perpendicular axes), causing the softened material to disperse and stick to the walls of the mold. In order to maintain even thickness throughout the part, the mold continues to rotate at all times during the heating phase and to avoid sagging or deformation also during the cooling phase.
Common examples of rotational molding include parts larger than 2’ such as containers, utility carts, storage bins, car parts, tanks (oil, septic, water) and leisure products such as kayaks.
Vacuum Molding
Vacuum molding is a process by which a sheet of plastic is heated until it becomes pliable, stretched onto a single-surface mold and forced against the mold by a vacuum to create a shape.
This process can also include thick-gauge thermoforming, a type of vacuum molding, that is known for producing a variety of products including disposable cups, containers, lids, trays, blisters, clam shells, and other products for the food, medical, and general retail industries.
Common products produced with the vacuum molding application include industrial containers and crates, pallets, exterior door panels, plastic totes, plastic trailers, passenger cabin window canopies for winged aircraft, and lawn mower hoods.
Would you like additional information about the plastic injection molding process and its capabilities? Contact our Application Engineers today at 586-598-4636 or sales@xcentricmold.com.