What is a Bridge Tool? Is there a Difference Between Prototype and Bridge Tools?
A bridge tool is often a prototype tool that produces production quality parts. The intent of a bridge tool is to provide a sufficient volume and production rate of molded products while hardend high productivity tools are being produced. This allows products to be brought to market sooner and decisions on when or if to commit to production tooling to be delayed. Both of these factors are incredibly valuable to our customers in markets where product cycles are becoming shorter. In many instances Xcentric’s customers elect to have us produce prototype, bridge, and production tooling to assure a seamless handoff between each phase.
At Xcentric, there is little difference between Prototype, Bridge or Production tooling. While other injection molding companies differentiate between mold types, we take an engineering approach to building all of our molds with production as the intent. During the engineering process, each mold is constructed and engineered based on annual volume, production rate, geometry, and complexity.
Due to our approach to the mold building process, we typically are able to achieve cost reductions beneficial to our customers. This is also attractive to customers who want to use their mold for a prototype and later decide they want to use it for bridge production or even high volume production.
What is Rapid Injection Tooling?
Simply put, Rapid Injection Molding and Tooling refers to building molds faster than traditional processes allow. Xcentric achieves speed through optimized processes and technology. Some companies claim rapid tooling and injection molding but sacrifice quality. Xcentric does not. In addition, others are usually limited to simple parts and little to no undercuts. Many cannot handle large projects. Also noteworthy, that their molds might have a limited life expectancy.
Are there Limitations to Rapid Injection Molding/Tooling?
At Xcentric, we do not cut out any process steps from conventional tooling or molding. Using our proprietary Process Engine, high quality mold materials and components, state–of–the–art equipment, a well trained staff, and streamlined process flow, we simply make high quality molds very quickly. As a result, it allows us the ability to call our injection molding process “rapid”.
Where there are limitations compared to very high volume production tooling is in production rate. Certain applications like caps and closures may require production tools with dozens of cavities, hot runner systems, and highly tuned processes to achieve extremely high parts per hour production rates not possible with our tooling approach. However it usually takes months to produce such a high speed tool, by which time we would have made hundreds of thousands of production quality parts to bring their product to market sooner.
Is Rapid Prototyping the same as 3D Printing/Additive Manufacturing?
Injection molding FAQs often include questions about rapid prototyping because it is a broad term used for many manufacturing processes to make parts quickly. Initially, 3D printing and other additive techniques were referred to as rapid prototyping. At Xcentric we offer our clients a range of solutions to get them prototype components with the appropriate material, physical, mechanical, optical, and aesthetic properties at competitive pricing.
We take into consideration the immediate and end use application of the prototype component to help select the best available process from a time, cost, and performance perspective. In some instances it is more time and cost effective to produce prototype and production parts with 3D Printing, sometimes prototypes with 3D Printing and validation with Rapid Injection Molding, and in some cases due to advancements in CAD and simulation, going directly to production injection molding relying on Xcentric’s advanced mold making and molding process engine.
We offer the following Rapid Prototyping services in order to better serve our customers throughout the manufacturing process from design to production:
What is the typical cost of Rapid Injection Molding/Tooling?
Due to Xcentric’s proprietary process, costs and lead times of our molds and injection molded parts are very competitive with domestic and internationally produced molds. Because every project is different and dependent on complexity, please request a quote and you will receive a custom quote prepared by our team within 24 hours.
A mold is automated by use of a slide and cam to remove the tool from the undercut in the part. Once the slide that forms the undercut is out of the way, the mold is free to open and eject the part.
Tool automation is very expensive and time consuming to design, however, when annual volumes and production rates are high, the cost is easily absorbed because of a much lower per piece price. Our quote engine and engineers will decide what the most cost-effective approach is for your project.
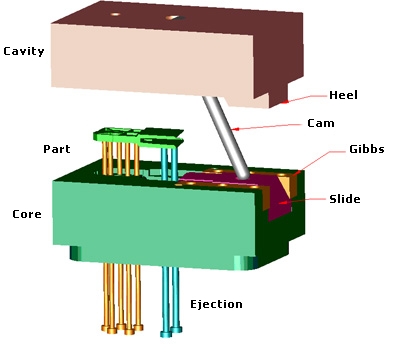
What is a Manual Tool?
Manual Molds that produce parts with undercuts such as windows or clip, require side action(s), before the part can be removed from the mold. Undercuts in the part can greatly increase the cost of tooling.
At Xcentric, we are able to manufacture what we call hand pulls (see illustration Below). Hand pulls are used to reduce the cost and delivery time of tooling. Incorporating hand pulls into the mold design requires a molding machine operator to run the parts. The operator must remove the part by hand and then reload the hand pulls back into the mold to make another part. This is a cost-effective approach for low-volume part runs and highly complex parts but will result in a higher per piece price.
Due to physical constraints within the mold body, parts with high complexity and multiple undercuts cannot easily be automated. When high volumes and a lower piece price are required, automation of the hand pulls may be possible. Our quote engine and sales engineers will determine what the most cost–effective approach is for your project.
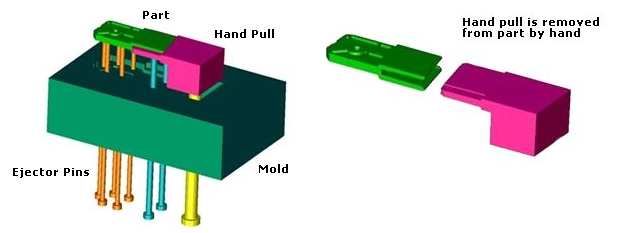
What is an Automatic Mold?
A mold is automated by use of a slide and cam to remove the tool from the undercut in the part. Once the slide that forms the undercut is out of the way, the mold is free to open and eject the part.
Tool automation is very expensive and time consuming to design, however, when annual volumes and production rates are high, the cost is easily absorbed because of a much lower per piece price. Our quote engine and engineers will decide what the most cost-effective approach is for your project.
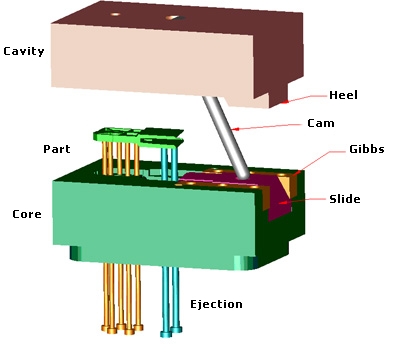
Experts in Design
Xcentric has served the quick-turn, plastic injection molding industry. With the advancement of in-house technologies, we now offer CNC Machining, Rapid Prototyping and 3D Printing Services in addition to our core injection molding service.
Start Your Quote