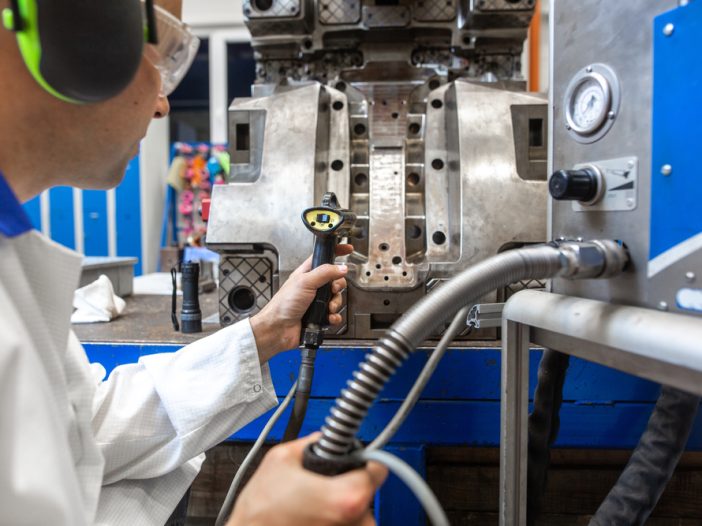
Typical Plastic Resins used in Injection Molding
Injection molding is used to make plastic products, but what is its purpose? Plastic industries need to concentrate on machine design and molding techniques that would provide the most appropriate and cost-effective ways to manufacture their products.
There are several types of injection molding. Molten thermoplastic is injected into a mold during injection molding. Plastic parts are most commonly manufactured using this process. Injection mold materials must generally meet the following requirements.
Metals are commonly used materials used in injection mold parts. Also, some of the shapes and sizes of the parts can be very complex. As a result, mold materials can easily be processed into the shape and precision required by drawings. This will help to shorten the production cycle and improve efficiency.
Surface abrasion resistance and the surface luster and accuracy of the plastic pieces have a direct relationship, especially when one –
- adds glass fiber
- use inorganic fillers
- color some plastics with pigments.
XCentricMold, a leader in rapid prototyping and injection molding, says that the materials are not wear-resistant; they will wear away and damage the quality of the parts. They contain plastic melt in the runner and the cavity in the high-speed flow.
A high degree of corrosion resistance, a number of resins, and additives react negatively with metal on the cavity surface, causing metal corrosion, peeling, surface deterioration, and a deterioration of plastic part quality. In order to protect the cavity from corrosion, it is best to use corrosion-resistant steel or to apply chromium plating and cymbal nickel treatment to the cavity surface.
Process of manufacturing injection molding molds
Plastic can be molded into various shapes with the help of rigid frames or molds. In addition to car parts, containers, signs, and other high-volume items, plastic molding techniques are also a popular manufacturing method.
Types of Molding Processes.
As part of the manufacturing process of plastic, molding is primarily used. The molding process used to form plastic into the desired shape is different because plastic is a synthetic material. One must manipulate and allow melting plastic to set before each process can take place.
Injection molding and extrusion are similar processes. A screw thread forces plastic granules through a die after they are heated in a hopper. The material is then cooled. It is only possible to vacuum form thin plastics and molds that do not have undercuts when using vacuum forming. Trimming the plastic to the desired shape is then possible.
Mold setup
Whether inserts are added by hand or robotically depends on the part. Hydraulic pressure closes the mold.
Plastic extrusion
Using a screw, small plastic pellets are heated and extruded through a heated chamber.
Molding
Injecting molten plastic into the mold is the next step.
Cooling and release
It cools until it becomes solid and is then ejected by either compressed air or mechanical means.
Post-processing
In most cases, the part is opened automatically as part of the mold opening process, including-
- Spruces
- runners
- flash (if applicable).
Injection molding can be replaced with what kind of plastic?
Deliver plastic to extremely complex and large or tiny items in a very controlled way. If tolerances are not too onerous, the alternatives available can be perfectly satisfactory if they come close.
Thermoforming and vacuuming
A thermoforming process involves laying plastic sheet material into a mold and squeezing it into the mold form. This is great for yogurt pots. You can make many yogurt pots by injection molding, even if you are not planning to make bazillions of them. In that case, the wastage may make it worthwhile to invest in the expensive tooling required.
Blow molding
This is a method for making hollow objects, typically bottles. But one also use to make car fuel tanks, which require welding two or more injection-molded parts to make each hollow piece. There is already a weakness in that weld line. When making truly seamless hollow pieces, blow molding is usually more effective than injection molding.
Rotational molding
Making large open or hollow elements, such as water troughs and kayaks, using this method is a fairly primitive method. We’ve seen some pretty intricate rotational molding examples, but they can’t match injection molding’s performance or tolerances.
Injection molding materials
As we’ve covered the specifics, we’ve added a few general qualities you’ll need in any material you want to inject. Are there any consequences to melting, pumping, and freezing the material without losing its performance?
It is acceptable for plastics and metals to meet this criterion if the criteria for “unacceptable loss of material performance” aren’t too severe. Due to their crystalline structure, metals are better in this criterion since they can regenerate as often as you desire.
Polymers (plastics) are generally permanently degraded upon heating. It is because they tend to break down into shorter chains of repeating molecules that are easier to pass through. Think about what happens when you take a fork and cut long spaghetti noodles into smaller segments once you find them tangling together in a big mass.
PE Material:
Thermoplastic materials such as polyethylene (PE) are very common. Different crystalline structures are available, including HDPE, LDPE, and LLDE. Many products are made from it, including –
- Bags
- plastic film
- milk buckets.
PP Material:
People use thermoplastic polymers, such as polypropylene (PP), widely in various applications. Using propylene as a monomer, it is polymerized through chain-growth polymerization. The polyolefin Polypropylene is partially crystalline and non-polar and belongs to the group of polyolefins. Although it is harder and more heat resistant than polyethylene, its properties are similar to those of polyethylene. The material has a high chemical resistance and is white and mechanically rugged.
PS Material:
As both a solid plastic and rigid foam material, polystyrene plastic (PS) is a naturally transparent thermoplastic used in injection molding. In addition, it is used in consumer products. PS plastic is also useful for commercial packaging applications.