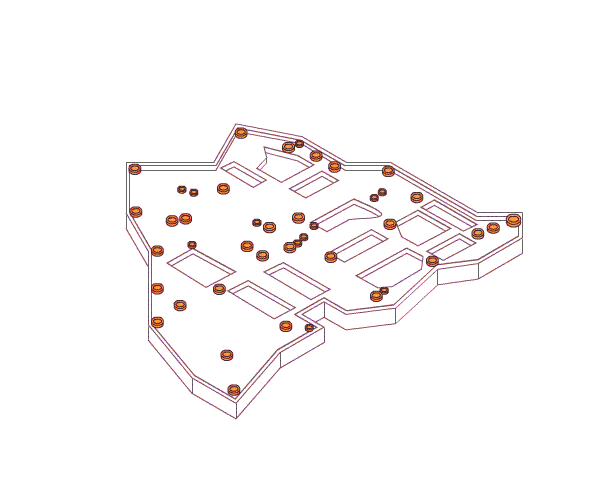
What is Complex Insert Molding?
Complex insert molding is sometimes utilized in order to get parts to market faster. It is a process in which plastic is injected into a mold that contains a pre-placed insert. The result of insert molding is a single molded plastic piece with an insert surrounded by the plastic.

Insert Molding Process
The insert molding process begins with the placement of inserts in exact positions within a mold. This placement can be done by a robot or a human. For exact placement, inserts are positioned on small metal locating pins within the bottom tool of the mold.
Support pins typically leave small holes. In some cases, overmolding is used to fill in the holes. In other cases, retractable pins are used. If retractable pins are utilized, pressure from the injected plastic will push the pins out of the mold, therefore, the pin holes will be filled during the plastic injection process.
After the mold is loaded with inserts, the mold closes and the plastic is pushed through the mold. Once the plastic has cooled, the mold opens and the part is ejected.
What are the benefits and challenges of Insert Molding?
Today’s Design Engineers are challenged to reduce costs, size and weight of parts or components while increasing part reliability.
Complex insert molding is utilized for many industries. This molding process offers some distinct benefits and potential challenges:
Benefits
- Reduces Post Molding Assembly
- Saves on assembly and labor costs. Many sizes and types of inserts can be placed directly into the mold before plastic injection, thus eliminating secondary operations and providing robust mating of the insert and plastic.
- Reduces Size and Weight
- Increased demand across several industries to convert from metal to plastic parts due to size and weight
- Metal to plastic conversion can make parts more efficient in a variety of ways
- Allows for lowering part weight
- Reduces production costs
- Can eliminate corrosion
- Increased Durability
- Enables Designers to integrate features that will make parts stronger, more durable and more reliable than native plastic areas.
- Enhanced Product Design
- Allows for integrating features not possible with plastic alone
- Increased Design Flexibility
- Part designs that are stronger and more durable
Potential Challenges
A variety of factors may pose potential issues in the process.
- Post processing
- Gamma sterilization
- Alcohol bath
- Molding issue
- Bosses could create sink or warp. Shrinkage will vary depending upon the amount of plastic placed in the inserts. Check with your plastics manufacturer on material shrink rates.
- No room in the plastic for inserts
Guidelines for Standard Molded Inserts
Inserts can be made of metals or different types of plastic. A wide range of metal components can be used in the insert molding process including limiters, fasteners, magnets, screens, tubes, clips, mounting brackets, screws and more. Components can be made from a variety of materials such as brass, copper, aluminum, stainless steel, nickel or bronze.
- Standard Molded Inserts
- Brass or steel threaded inserts
- Closed hole, open-ended
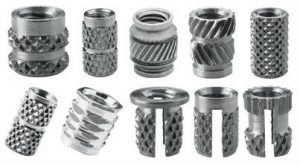
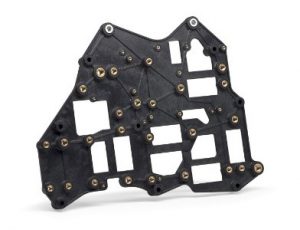
A good design includes ensuring proper adherence of the metal in the plastic part. In some cases, inserts need to be heated prior to molding in order to reduce thermal differences between the metal and the plastic.
- Inserts should be rounded (no sharp corners). Use an undercut for pull-out strength.
- Insert should protrude min. 0.4mm into the mold cavity. Depth of mold beneath should = 1/6 of insert diameter to avoid sink.
- Boss diameter should be 1.5 times the insert diameter
Guidelines for Custom Molded Inserts
Custom molded inserts can include:
- Bushings
- Connectors
- Drill bits/guides
- Needles
- Tubing
- Magnets (demagnatized)
- Hand loads
- Horizontal
Follow Standard Design Considerations
- Shut off is Critical
- Tight grip of the insert needed within a cavity/core or hand load within the tool
- If not a tight grip, there must be shut-off with cavity and core together
- Must have contact point to be loaded on cavity/core or hand load so that tool can close and insert stays in place
- Problematic inserts – inserts that move under pressure
- Thin metal insert wires
- Small electrical connectors
- Thin stamped inserts
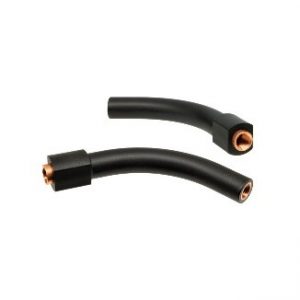
Material Considerations – Part
Just about any plastic material may be used for insert molding including general purpose materials to engineering grade materials.
- Utilize stress chain chart
- Materials with low shrink rate work better
- Toughened grade resins have higher elongation and greater resistance to cracking
- Good – nylon, polycarbonate
- Bad – Polypropylene, polyethylene
Material Considerations – Inserts
Inserts may be plastic or metal parts. Standard materials include:
- Brass
- Stainless Steel
- Ceramic
- Custom
- Aluminum
- Ceramic
- Copper
- Magnets
Any material that can withstand the pressure and temperature of the injection molding process.
Industry Applications
There are many industries that use insert molding in their part designs. Several industries and examples include:
- Medical-medical and surgical devices
- Aerospace-aircraft controls, navigation/guidance systems
- Electronics-sensors, computer housings
- Consumer Products-HVAC systems and electronic components
- Automotive-parts to reduce weight and assist with fuel economy
- Agriculture-land and aeration systems
- Communications-filters
- Appliance-connectors
Summary
Complex insert molding allows the inclusion of inserts into a plastic part.
- Insert Molding can reduce assembly and weight
- Be aware of potential issues
- Standard Molded Inserts
- Ensure they are rounded
- Depth of mold = 1/6 diameter of insert
- Boss is 1.5 times insert diameter
- Custom Molded Inserts
- Follow Tips for Standard
- Shut off is critical
- Molding Materials
- Low shrink rate is better
- Nylons, Polycarbonates, ABS & PC/ABS are good
- Insert Materials
- Brass, Stainless Steel, Ceramic, Copper, etc.
- Materials that can withstand the injection process
There are a variety of industries where insert molding is used in part design.
Interested in obtaining more advice? Reach a Technical Engineer at sales@xcentricmold.com or call (586) 589-4636.
Read more about injection molding best practices.