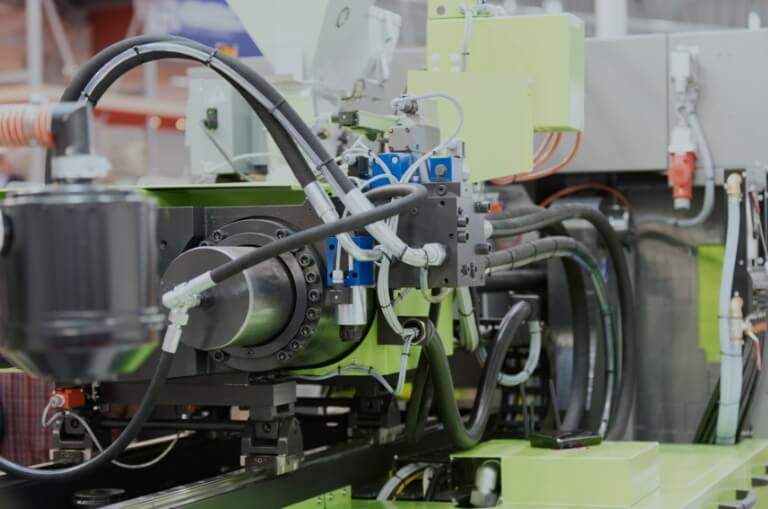
PEEK Properties, Characteristics, And Applications
Product developers and engineers are often overwhelmed by the number of injection molding plastics they must choose from to find just the right material to manufacture with.
There are thousands of plastic variations available, from everyday commodity plastics to high-performance polymers used in very demanding operating environments. At Xcentric, we have more than 40 resins in stock to choose from and take particular care in advising our clients on material selection.
Among the small number of high-performance polymers, the PAEK (PolyArylEtherKetone) family leads the way, and, among these, PEEK (PolyEtherEtherKetone) is the most popular.
Here is why: Many high-performance polymers can stand up to one or two requirements, either the ability to withstand extreme temperature or chemical exposure. However, most of these fall below expectations when it comes to other demands, such as wear-resistance or mechanical strength.
PEEK, however, possesses several of these properties: including mechanical strength, wear-resistance, heat resistance, and chemical resistance. It is easily processed and recyclable.
Its other properties include electrical insulation, corrosion resistance, and high purity.
And because PEEK can be mass-produced by injection molding without involving the machining of metals and the curing of thermosets, there are fewer processing steps. This results in time and cost advantages.
PEEK often outperforms metal when used in harsh environments. This makes it a popular choice when manufacturing aerospace and automotive components, medical devices, machinery parts, semiconductors, and electrical and electronic machinery.
Examples of PEEK Components:
- Automotive: Engine parts, variable speed transmission parts, steering parts, brake components.
- Office machinery: Copier claws, special heat-resistant bearings, chains, gears.
- Medical device: Endoscope parts and dental cleaners, implants, surgical devices, joint replacement.
- Aerospace: Electrical insulators and isolators, battery connectors, external light housings, gaskets, seals, fittings, brackets, clamps, and thermal acoustic insulation.
This is what our experts at Xcentric think you should know about PEEK to help you decide whether it is the right material for your needs.
Properties of PEEK Plastic
PEEK is a semi-crystalline, opaque material belonging to the PolyKetone family of polymers called PAEK, which comprises aryl, ether, and ketone molecule groups. The aryl and ketone portions of its build-up give PEEK rigidity and stiffness, which means good mechanical performance and a high melting point. The ether group in PEEK lends flexibility (making it tough) and renders it unreactive (providing resistance to chemical exposure).
Let us take a closer look at its properties and how it behaves and influences material selection in various industries:
- High heat resistance. Tests show that PEEK has a high melting point of 341°C, high glass transition temperature of 143°C, and a continuous use temperature of up to 260°C. This has led to its wide use in thermally aggressive environments such as oil and gas, and automotive industries.
- Chemical and corrosion resistance. PEEK is highly resistant to water and many solvents (even when subjected to them in high-temperature and high-pressure steam conditions). Therefore, it can withstand chemically aggressive conditions in the oil and gas industry—in sub-sea pipes, gears, and machinery. It can also stand up against jet fuel, hydraulic fluids, and de-icers in the aerospace industry.
- Wear-resistance. Tests show PEEK is more durable than many other polymers and even some metals. PEEK can withstand high loading at elevated temperatures without permanent deformation, also known as creep. It also has a low friction coefficient, which means less wear, noise, vibration, and emissions. This makes it a great material for use in car parts. Another measure of wear is fatigue resulting from repeated pressure and stress, and PEEK performs exceptionally well here too. It is also lighter than comparable metals, making it popular in the automotive and aerospace industries as it improves a vehicle’s energy efficiency. Its exceptional wear-resistance makes PEEK highly valuable in the production of medical implants as well.
- Biocompatibility. PEEK is not harmful or toxic to living tissue and can perform consistently inside the human body for lengthy periods of time. This characteristic makes it popular for use in medical device parts and implants. However, due to its biologically inert chemical structure, PEEK has poor bonding ability to bone tissue implanted in vivo.
- Tensile strength. When reinforced with carbon fibers, PEEK-based materials can reach a tensile strength of 29000psi at up to 299°C. This makes it a stronger and stiffer option than nylons, acetal (PolyOxyMethylene or POM), polyesters, and polycarbonates.
- Low flammability. PEEK, which has a UL 94 V-0 flammability rating, resists combustion up to almost 600°C. It also emits little smoke even when made to burn at extreme temperatures. This is one reason it is commonly used when manufacturing parts for commercial aircraft.
- Good insulation. PEEK has high volume and surface resistivity to maintain good insulation performance even under significant temperature and environmental changes.
- Recyclable. PEEK’s molecules are very stable, so it can be reprocessed multiple times without affecting its properties. This enables manufacturers to reduce waste management costs and meet sustainability goals.
What are the Types of PEEK Plastic?
PEEK comes in five grades based on composition and variances in properties that influence which applications it is best suited for:
- Unfilled PEEK is not reinforced with any other material and is the most basic version of this polymer. It is the most chemically resistant type.
- Carbon fiber-reinforced PEEK has 30% carbon-filled fibers added to it and is the strongest and stiffest type. It is also 7% lighter than glass-reinforced PEEK.
- Glass fiber reinforced PEEK has 30% glass fiber mixed in and is stronger and stiffer than unfilled PEEK. It also provides excellent electrical and thermal insulation.
- Bearing PEEK is filled with 20% PTFE and carbon-reinforced with graphite to lower the friction coefficient, offering improved wear-resistance and higher frictional heat capability.
- Static dissipative, metal detectable and x-ray detectable PEEK, and custom makes. These PEEK types have been created to meet customers’ specific requirements for one or more application capabilities. For example, static dissipative PEEK is designed to be safe for use in atmospheres where non-conductive materials are required.
Special Considerations for PEEK Injection Molding
While PEEK scores many performance points, its use does come with challenges.
- High price. PEEK costs more than standard engineering plastic materials.
- PEEK’s stiffness could mean certain levels of contouring may be difficult or impossible to achieve.
- Depending on its type, PEEK comes attached with some acids such as concentrated sulphuric, nitric, or chromic acid. This makes it less desirable for certain applications.
- PEEK has low resistance to UV light, but this weakness can be countered by adding a carbon additive to the material formulation to provide UV resistance.
Is PEEK the Best Material for Your Needs?
If you are looking for an injection molding material solution that strikes a balance between your performance needs, budget, and environmental and sustainability goals, PEEK will top the shortlist (or come close!)
But is it for you?
While PEEK will enable you to make lighter, stronger, and more chemically resistant parts that will last longer, you need to evaluate how much of a return on your investment this material will get you, considering its additional cost. Talking to a material selection expert from Xcentric will help you decide. We will take you through an efficient design and manufacturing process that will bring even your most complex products to market in weeks.
Xcentric will:
If you have a project you need help with, submit it here, and our team will be happy to provide expert advice.
About Xcentric
Founded in 1996, Xcentric Mold & Engineering is an innovator of on-demand digital manufacturing and continues to lead advances in injection molding and rapid prototyping. We know what it takes to deliver a high quality product on time and on budget. Xcentric is engineered to be nimble, employs a team of experts in injection molding, and takes an engineer centric approach to everything we do. Tens of thousands of product developers and engineers across North America trust Xcentric to bring their products to life.
Learn more about what Xcentric can do for you here.
Questions? Contact our friendly sales team here or on 586-598-4636.